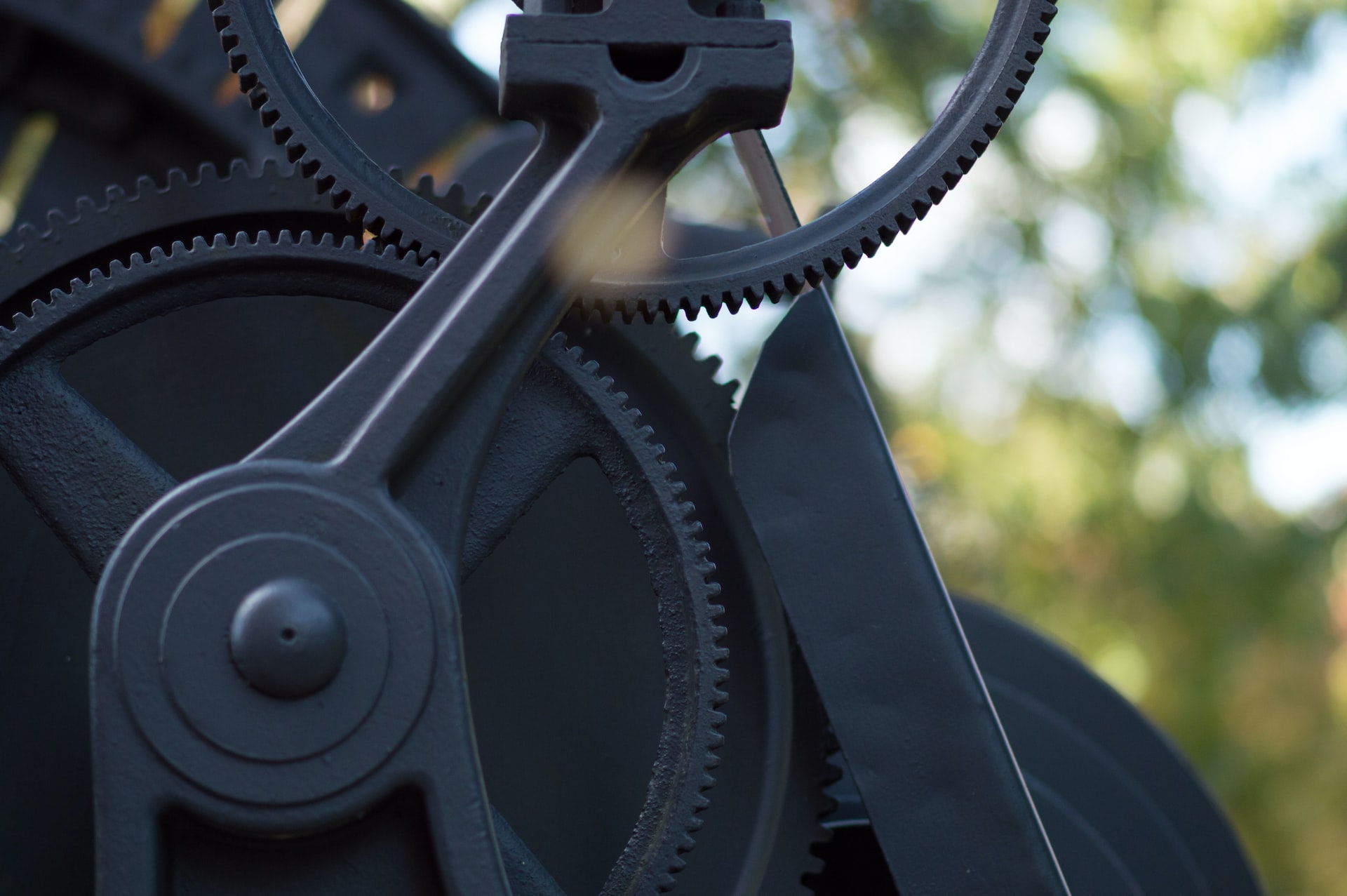
How to Take Proper Care of Your Equipment?
Equipment that is well-maintained will rarely break down, this increases uptime, the useful life will be extended, maintenance expenses are lowered, and ultimately profits are boosted. Whether a car, industrial machine, hand tool, or other forms of the machine operates more effectively when it is well-maintained. The mechanisms must work harder to produce the same effects when the air filters are clogged. An engine is not as well lubricated by dirty oil as by clean oil. Fluid usage increases due to worn belts slipping and hose leaks developing. Poor maintenance of equipment results in operational inefficiencies, which can harm run time, output or performance, and cost.
Seal Your Equipment
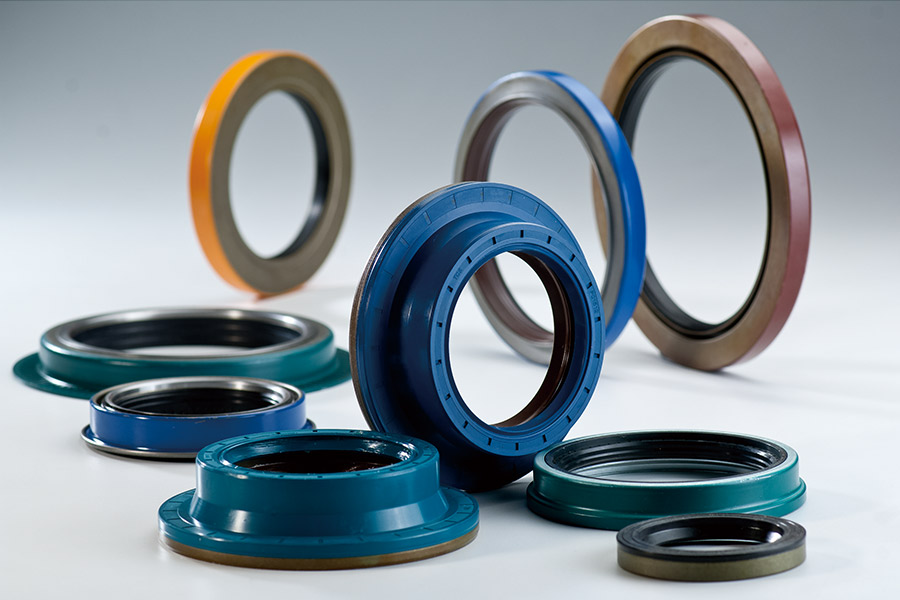
The selection of seals is hampered by a lack of expertise and data. Before settling on a seal, it’s essential to think about the intended use, the typical working environment, and any other scenarios. For instance, choosing industrial seals that can function in hot water would seem simple because water isn’t a particularly challenging medium. However, this presumption fails if the application is boiler-feed water. Hot water over 190 degrees Fahrenheit is too hot to lubricate and cool seal faces effectively. As a result, the sealing process becomes weakened due to increased wear on the joining sides, and the seal ultimately fails before it should.
Know Your Equipment
Ensure you and any other operators know how a piece of equipment operates and what it is used for before using it. If you can, conduct a test run. The equipment’s warranty details, anticipated lifecycle, age, and any known problems, you should be aware of them. As a result, it will be used safely and correctly, and you will know what to anticipate from it and what to do if it doesn’t meet your expectations.
Check Frequently
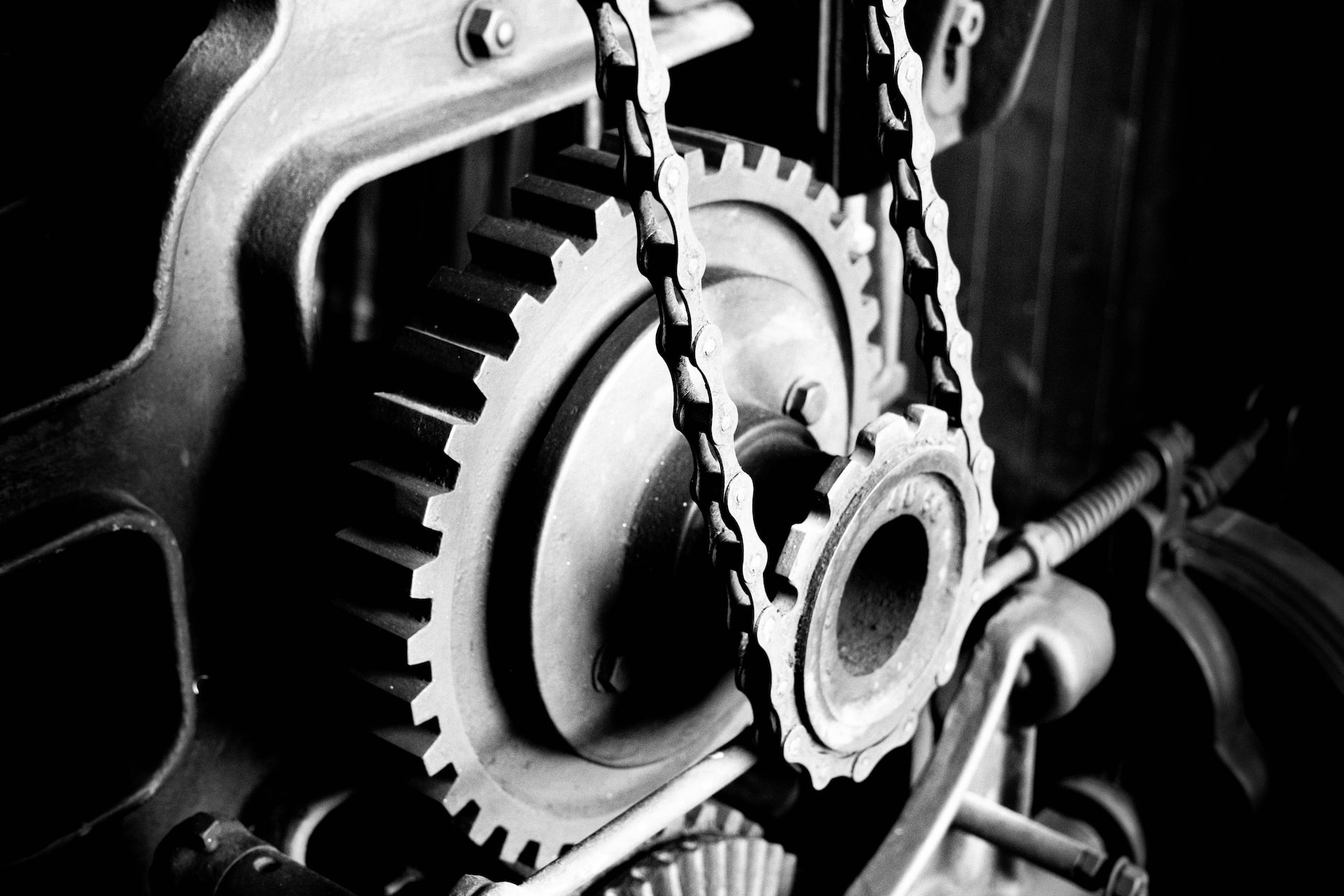
Frequent equipment inspections might reveal irregularities and problems not seen during routine use. Before the problem worsens and damages the equipment or becomes unsafe, repair or replacement can then be arranged. Depending on the equipment’s nature, a competent engineer may need to inspect it regularly and properly. Usually, your supplier or the manufacturer can advise on how these inspections should be organized.
Maintain Equipment Regularly and According to a Schedule
When something goes wrong, it is typically crucial to correct it as soon as possible. Proper maintenance can prevent needless, high expenditures. You find that keeping track of maintenance is made much easier by making a simple maintenance plan that lists what has been maintained and when and when it is due again. It can also aid in limiting routine inspections.
Replace Components as Necessary
Smaller parts on heavily utilized equipment will wear out and must be replaced to maintain their functioning as efficiently as possible. It is best to replace them as soon as possible because doing so frequently stops other parts from getting damaged or worn out. To avoid equipment downtime, it’s a good idea to keep a modest stock of popular parts that you frequently use on hand. this will save you in case of an emergency breakdown with your equipment.
Check for Indications of Tear and Wear
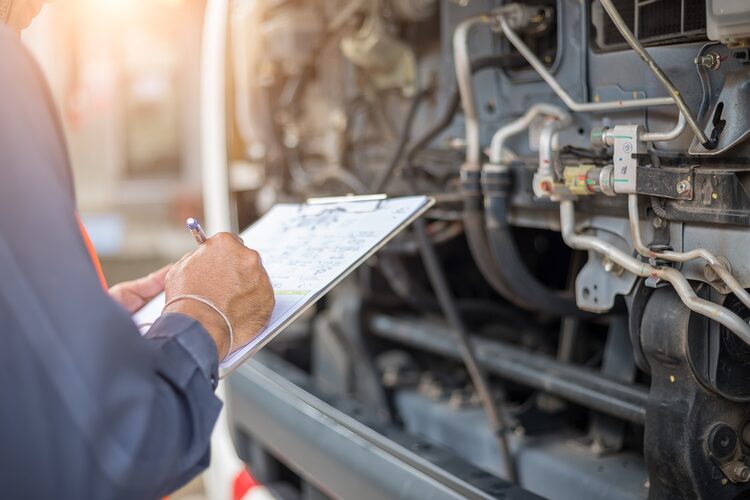
One of the most significant ways to ensure that your equipment lasts as long as possible is to inspect it regularly for damage and signs of wear. Heavy machinery can break down due to high heat, shock, and friction. Unprofessional operations or unexpected events may cause shock. High temperatures might result from overwork and lack of lubrication. Whenever you find a worn part in heavy machinery, please don’t wait for routine maintenance to replace it; do it immediately.
Performance Monitoring
Being knowledgeable of and prepared for the effects of weather, geography, and other environmental factors on your assets is essential. Your equipment’s performance should be monitored to forecast when it might break down and help you schedule its replacement. For a globally dispersed fleet, this is of paramount importance. Manufacturing equipment fleets can benefit significantly from the use of equipment management software. The correct software will allow you to keep tabs on your assets in real-time, plan for periodic inspections, and notify you when it’s time to work on a particular piece of machinery. In addition, predictive data is another advantage of equipment maintenance software.
Clean Regularly
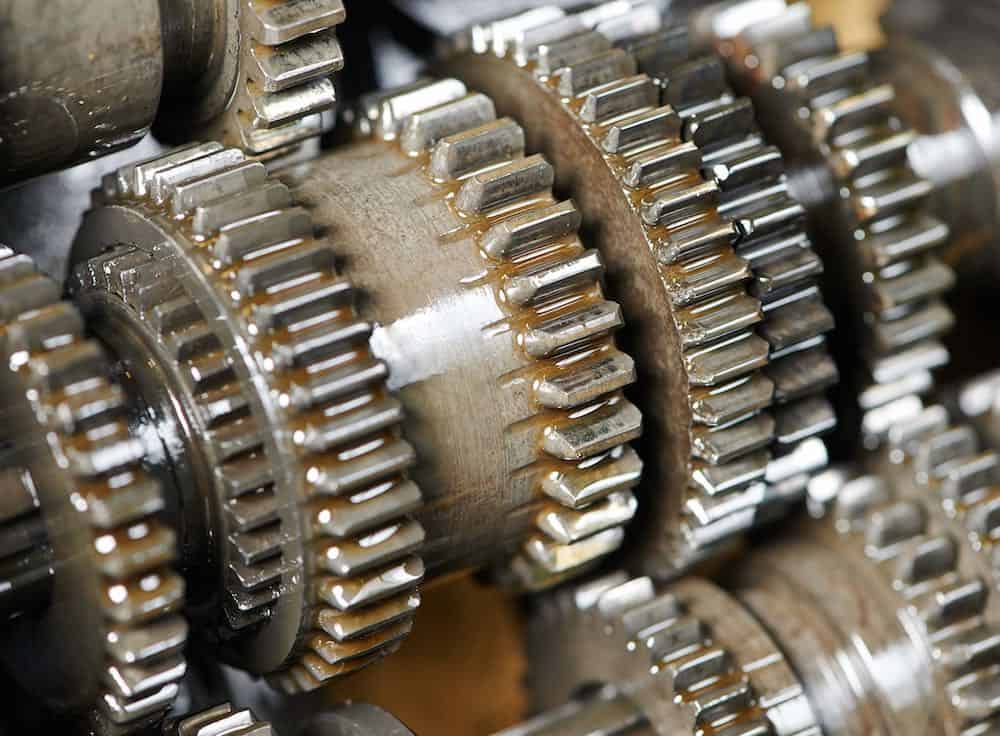
Cleaning power tools before putting them away at night is integral to routine equipment maintenance. A quality cleaning cloth will allow you to remove dust and other debris from the exterior casing. Compressed air is the most excellent option for cleaning the particles from the tool’s vents; using a brush to clean the tool’s exhaust vents could drive the dirt further into the equipment, leading to more significant harm. You should invest in cleaning tools that will ensure your equipment is not damaged in the process of cleaning. For metallic parts, avoid cleaning with water as this would cause rusting, or if you have to clean with water, grease afterward.
Treatment for Batteries
Current power tool standards necessitate the use of lithium-ion batteries. Keeping the temperature of your lithium-ion battery under control is crucial to its long life and performance. Batteries can be permanently damaged by being allowed to overheat. Keep your batteries out of extreme heat, such as the enclosed back of a vehicle, and keep them in an excellent, dry spot. Keep the battery from dying fully before charging it again.
The equipment’s usable life and value retention both increase with proper maintenance. Equipment’s functional life can be extended by three to five years, translating into an additional three to five years of revenue from the same gear. When a business seeks commercial equipment finance, having well-maintained equipment might be advantageous. Using equipment as collateral for a loan can be very advantageous when a firm wants to borrow money, whether to finance corporate operations, consolidate debt, or buy or lease equipment. An equipment lending company specializing in collateral loans will consider the equity in that equipment when determining your ability to borrow money. Your ability to borrow money will increase as your equipment’s value rises and your equity in that equipment increases.